In todays fast-paced manufacturing landscape, the demand for precision and customization has led many industries to explore the advantages of custom CNC milling parts. These intricately designed components, crafted using advanced computer-controlled machinery, promise not only enhanced accuracy but also the ability to tailor products to specific needs.
However, as with any manufacturing approach, there are both benefits and drawbacks to consider. On one hand, custom CNC milling offers unmatched design flexibility and the potential for reduced waste, enabling businesses to push the boundaries of innovation.
On the other hand, challenges such as higher initial costs and longer lead times can complicate the decision-making process. As we delve deeper into the intricacies of custom CNC milling, a balanced perspective on its pros and cons becomes essential for informed choices in production strategies.
Advantages of Custom CNC Milling Parts

Custom cnc milling parts offer a plethora of advantages that can significantly enhance both production efficiency and product quality. First and foremost, they allow for precise tailoring to meet specific project requirements, enabling intricate designs and complex geometries that standard parts simply cannot achieve.
This precision fosters improved compatibility with existing components, reducing the need for costly modifications down the line. Furthermore, the efficiency of CNC milling processes translates to quicker turnaround times, which is vital in todays fast-paced market.
Manufacturers also enjoy the flexibility of materials—ranging from metals to plastics—allowing them to choose the best fit for performance and durability. Not to mention, the consistency in production minimizes waste and maximizes resource utilization, ultimately leading to cost savings.
In a landscape where customization is increasingly vital, the benefits of custom CNC milling parts can be the key differentiator for companies striving to innovate and stay ahead of the competition.
Disadvantages of Custom CNC Milling Parts
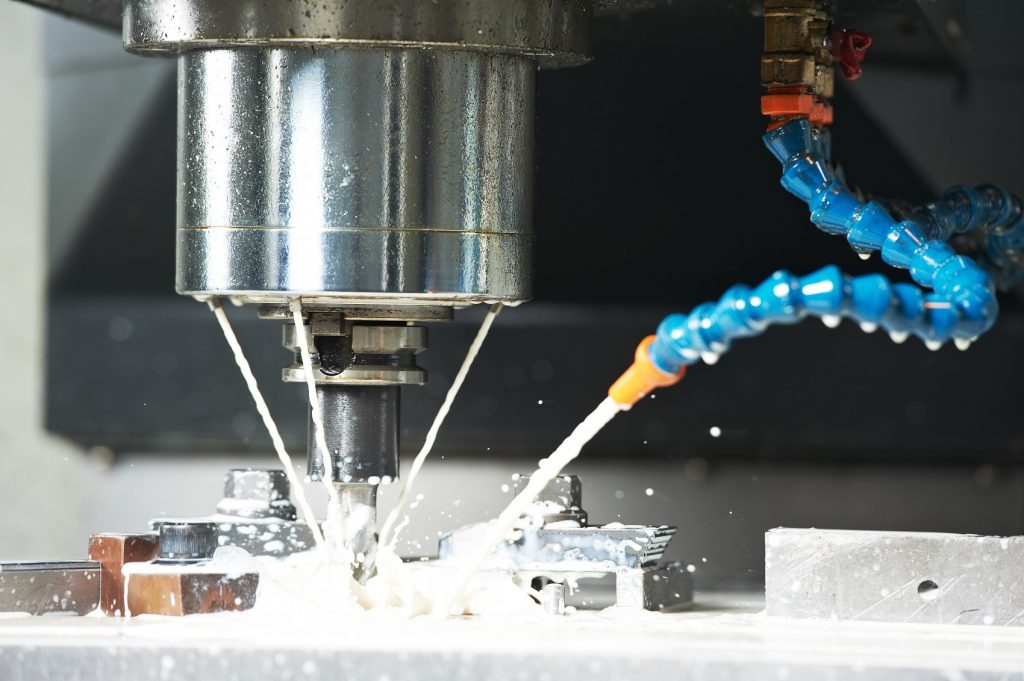
While custom CNC milling parts offer many advantages, they also come with notable disadvantages that can impact overall project viability. Firstly, the initial setup cost can be considerably high; designing and programming the CNC machine requires skilled labor and specialized software, which can inflate the budget—especially for small production runs.
Moreover, lead times can extend significantly, as intricate designs often necessitate prototyping and iterative adjustments before reaching the final product. This delay could hinder project timelines, particularly in fast-paced industries.
Additionally, since parts are tailored specifically to certain applications, the risk of obsolescence increases, rendering them unusable if project specifications change. Finally, there’s the learning curve associated with operating advanced CNC machines, as even minor programming errors can lead to costly material waste or defective parts.
In short, while the allure of custom CNC milling is strong, it is essential to weigh these drawbacks carefully against your project goals.
Comparing Custom CNC Milling to Other Manufacturing Methods
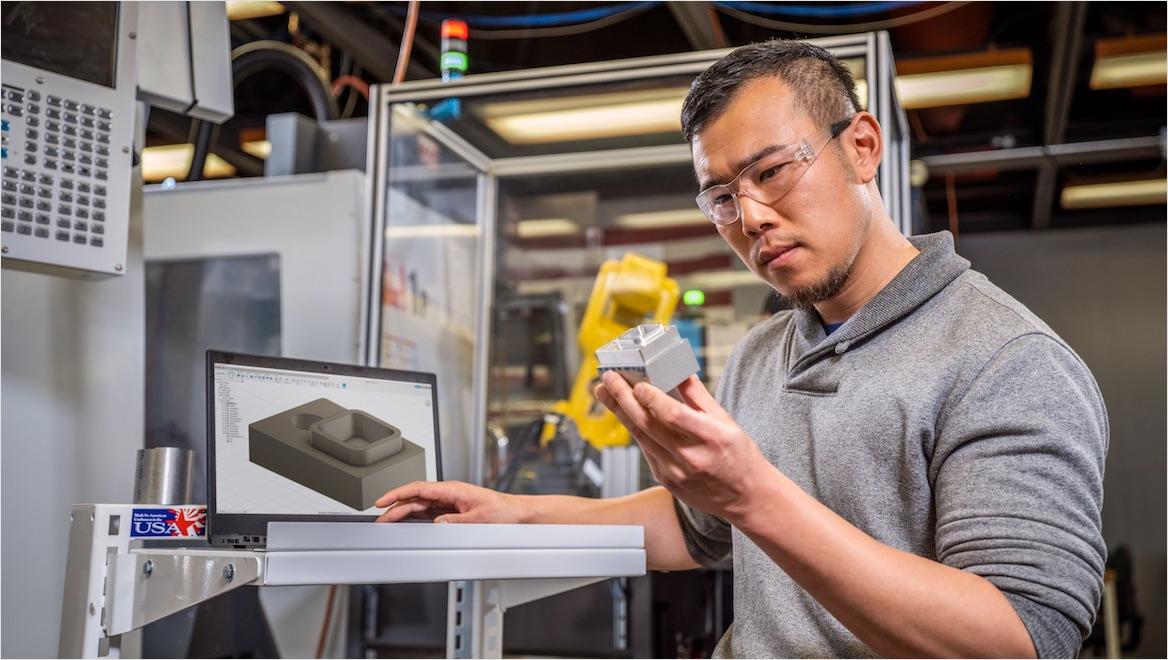
When comparing custom CNC milling to traditional manufacturing methods, such as injection molding or manual machining, distinct advantages and disadvantages emerge. CNC milling stands out for its unparalleled precision and ability to produce intricate designs with tight tolerances, making it ideal for complex geometries that would challenge other processes.
Moreover, the adaptability of CNC machines allows for quick alterations and iterations, facilitating rapid prototyping without the hefty setup costs associated with molds in injection molding. Conversely, while CNC milling excels at small to medium production runs, it may not be as cost-effective for large quantities—where injection molding shines due to its efficiency in mass production.
Additionally, manual machining can offer a personalized, hands-on approach that some niche markets still value, yet it often lacks the speed and consistency provided by CNC technology. In essence, the choice between these methods hinges on the specific project requirements, production volume, and budget considerations, underscoring the nuanced landscape of manufacturing options available today.
Conclusion
In conclusion, the decision to utilize custom CNC milling parts in manufacturing processes requires careful consideration of both their advantages and disadvantages. On one hand, the precision and flexibility offered by CNC milling can significantly enhance product quality and efficiency, allowing for intricate designs that may otherwise be unattainable.
On the other hand, factors such as initial setup costs, longer lead times for production, and the need for skilled operators can pose challenges for businesses. Ultimately, weighing these pros and cons enables companies to determine whether custom CNC milling aligns with their operational objectives and resource capabilities, ensuring informed decisions that can drive their success in a competitive market.